WOLFPAK™ Capes Medical
Decrease error rate and improve efficiency
01 Goal
Improve efficiency and reduce paper useage
Paper picking slips were removed and replaced with WolfPak Scan Pick.
Each item in an order would direct warehouse staff to the exact location in the warehouse.
Resulted in a reduction in time wasted by wandering around looking for stock.
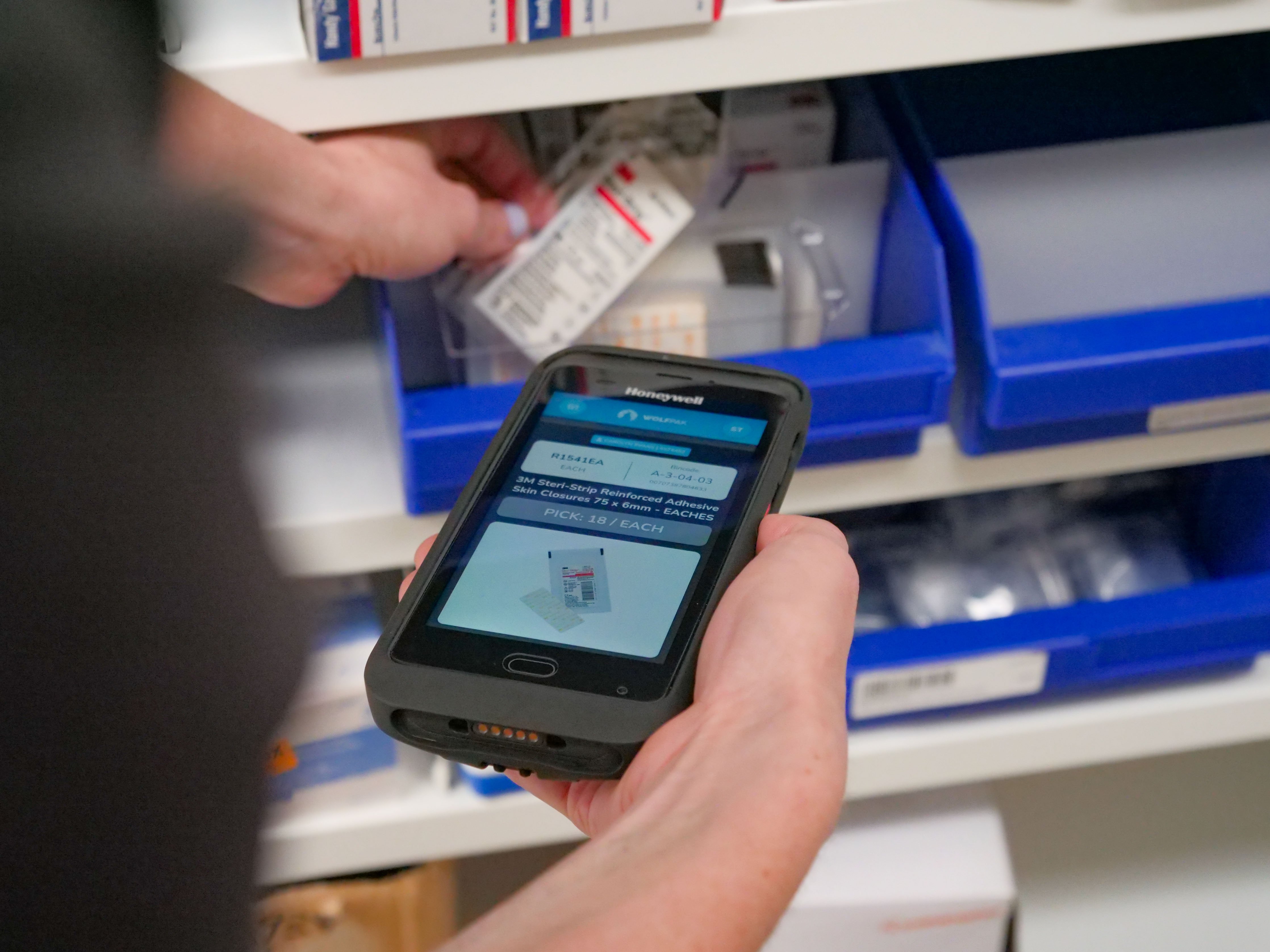

02 Goal
Gain an FTE without hiring
By decreasing wasted time taking multiple trips around the warehouse and reducing picking errors,
the challenge to gain an extra FTE of time from staff was achievable.
Adding more staff accentuated existing problems, so a alternate solution was required to realign.
WOLFPAK™ Capes Medical
Key Factors To Success
01 | FACTORS TO SUCCESS
The Barcode Scanner
Honeywell® CT40
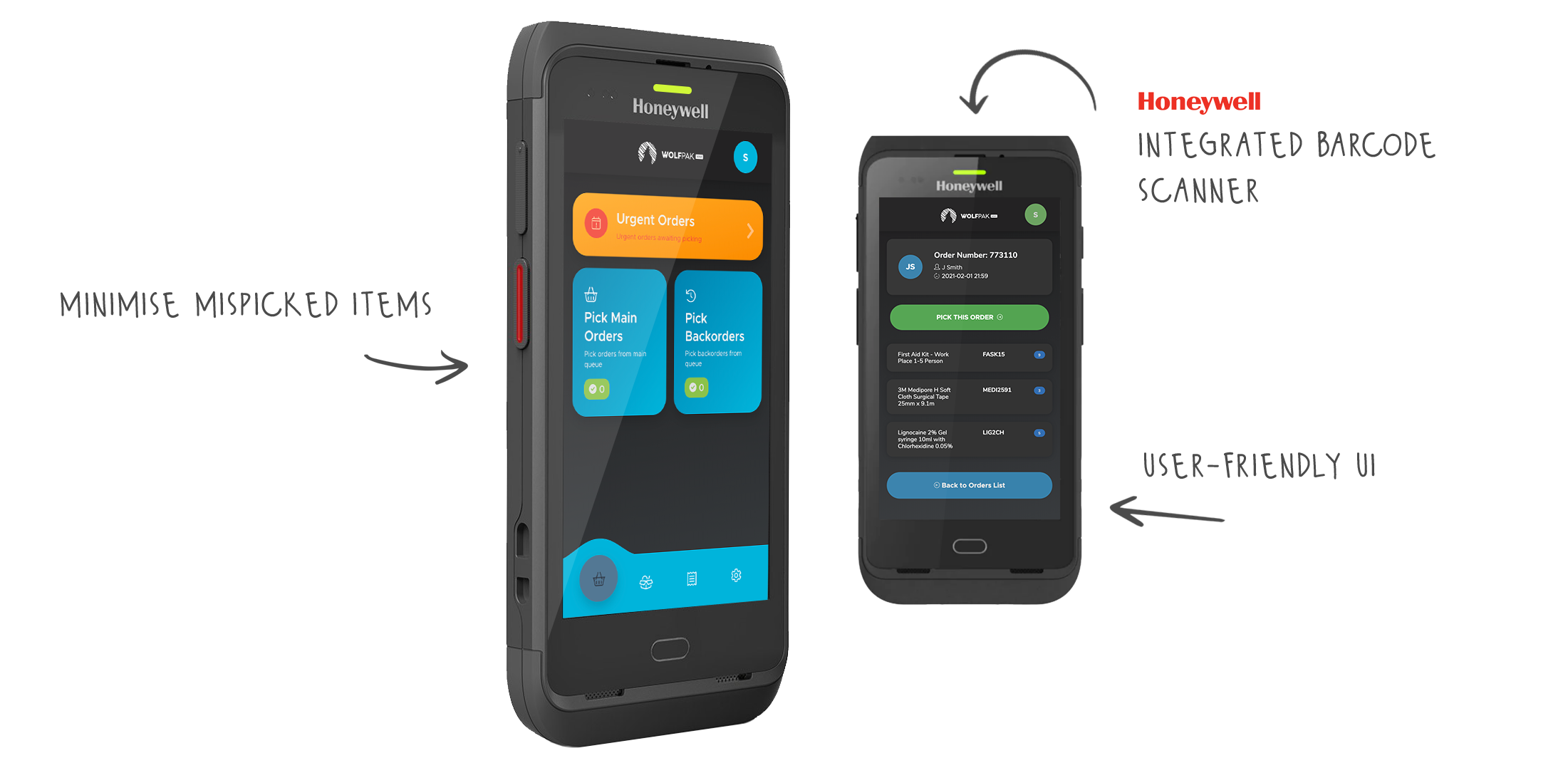
Scanning barcodes eliminates mis-picked products, but what about data consistency issues? especially in early phases where data is most likely to be incorrect?
WolfPak introduced a supervisor report showing managers Who, When and What was being overriden and incorrectly scanned.
This enabled the data trend to be assessed against all possible causes - staff laziness, incorrectly barcoded products, or no barcode present.
Management can easly view and solve problematic products.
Upon reseting a barcode, the supervisor can tag the product in the report as fixed to enable alerting if the issue reoccurs.
The Honeywell CT40 boasts all day battery life and can be returned to the charging dock at the end of the shift.
02 | FACTORS TO SUCCESS
SPEED vs ACCURACY
WolfPak Scan Pick & Pack
The goal is to streamline the process and eliminate as many steps and actions as possible to allow the user to move products from the shelf to the customer.
However, this poses risks of inaccuracy. For example
SPEED
The fastest process to pack 10X of an item is to scan the item, and tap yes 10 have been packed.
but..
What if only 9 were picked originally?
vs
Accuracy
The most accurate way would be to scan each individual item so the system can count for you.
but..
What if there are 83 items?
WolfPak Balances the Risk
WolfPak utilizes a number of strategies to assess the risk of a pick, allowing the "lower risk" picks to be processed faster while concentrating on the "higher risk" counterparts.
Recommendations are provided out of the box, however administration configuration is provided.